Compact AMR for Efficient Production and Logistics
24th January 2025
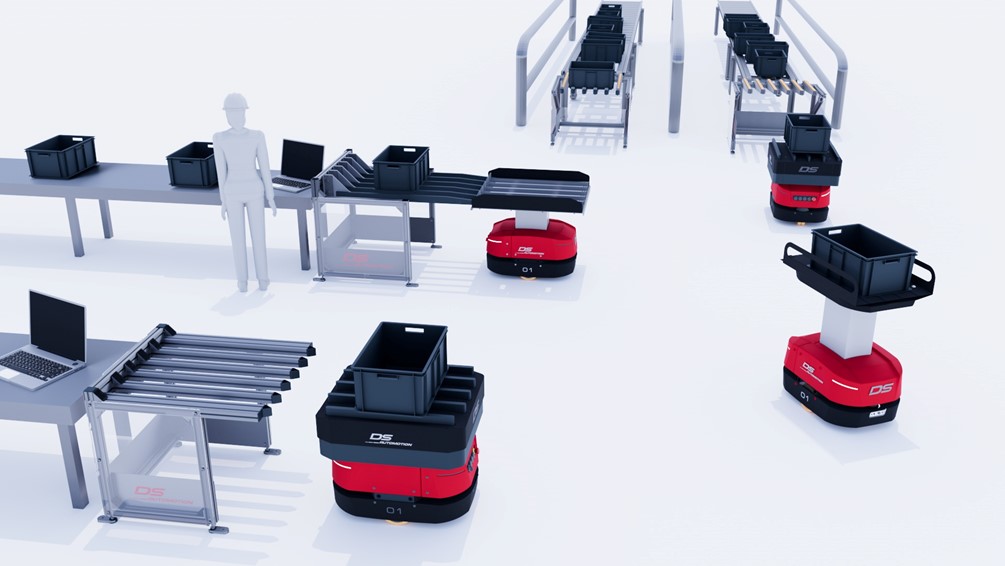
With AMY, a compact AMR for loads up to 25 kg / 55 lbs., and the fleet manager NAVIOS, DS Automotion will be presenting groundbreaking concepts and solutions for production and logistics for any company size at LogiMAT 2025 in Stuttgart. Trade show visitors have the opportunity to experience the new concepts for small load transports with AMY in action both on-site and providing an interactive experience for visitors to try out our fleet management system, NAVIOS.
They are in operation around the clock.They take over precise delivery tasks in the production process, relieve human needs, and ensure on time and precise workflows. They can be adapted in various production areas.
At LogiMAT 2025 from March 11 to 13 in Stuttgart, visitors can take a close look at these solutions with the AMR AMY in live operation. Trade fair visitors can also gain detailed insights into the fleet management NAVIOS – highlighting features how intuitive and user-friendly its cockpit is to operate, and how flexible the layout can be configured, tested by interested parties through test programming at the trade show.
Efficiency booster for small parts handling
AMY was specifically designed for use in industrial production and intralogistics processes and impresses with its quite simple operation and high flexibility. Through a unique transfer concept with an active lift table, sources, and sinks can be implemented as passive stations. This makes cost-effective implementation and scaling in existing systems easier than ever before. The smart control software developed by DS Automotion itself enables rapid commissioning – individually or in swarms.
The AMR can operate completely autonomously or follow a virtual track avoid unexpected obstacles. In addition, like all current vehicles offerings from DS Automotion, AMY is equipped with a VDA-5050 interface and can process files with the Layout Interchange Format (LIF). Under the fleet manager NAVIOS from DS Automotion, AMY can also be operated in mixed mode with other vehicles from the leading manufacturer of mobile robotics for in-house logistics and assembly applications. This makes AMY particularly suitable as a cost-effective addition to existing systems.
Thanks to the three different load handling devices (LHD), which can be implemented depending on the complexity at the customer – even in existing infrastructures – AMY proves to be a versatile AMR for numerous applications. The first variant is a passive LHD that works with the help of gravity. The advantage of this variant is that the LHD does not require sensors or drives. This makes it particularly simple and cost-effective. It works together with the appropriate transfer station, which also does not require sensors. This makes it ideal for applications where the material is provided independently of the vehicle.
The second LHD variant can also handle gravity roller conveyors and belt conveyors. This allows for easy connection to conveyor technology. There are also passive transfer stations for this system. The third option is a platform for manual loading and unloading. For this purpose, the vehicle is called to stations where the user manually places the load and then sends AMY on to next destination. For all three variants, a suitable web interface is available for operating the mobile robots: from generating the transport order to calling and acknowledging the vehicle.
NAVIOS — the holistic fleet manager
The key to optimizing and automating processes in production and logistics lies in an efficient fleet manager. NAVIOS from DS Automotion offers customers the opportunity to efficiently control their vehicle fleet – whether AGVs or AMRs. Thanks to an intuitive user interface and flexible layout configuration, users can easily and individually adapt their operations. Thanks to VDA-5050 compatibility, seamless communication between all mobile robots is also possible. The layout design of the driving course is visualized using a navigation map. The integrated route planning tool ensures maximum efficiency. This means that users can change the layout during operation, and the vehicles automatically receive the updated conditions. Users have access to extensive, meaningful analysis functions around the mobile robots and material handling.
similar news